Section VIII - Top Overhaul
1. Top Overhaul
(1) By top overhaul is meant the lapping of valves and the making of
necessary repairs of those parts on the crankcase which are accessible without
disassembling the crankcase. It includes the removal of cylinders,
pistons, piston rings and valve gear for replacement or service.
(2) The need for a top overhaul is usually indicated by not being able to get
the required engine speed with full open throttle while the airplane is on the
ground. It is also indicated by excessive oil consumption.
Note |
Winds, and extremes in humidity, temperature or barometer, due to
atmospheric conditions or altitudes will cause variations in propeller
speed. Loses or gains in propeller R.P.M.'s can be partially accounted
for by taking into consideration such temperature, barometer or humidity
extremes. It is therefore advisable to have mean ground temperature and
operating conditions when checking top overhaul need by means of propeller
R.P.M. at full throttle. It must be particularly kept in mind that
observed R.P.M. is considerably lower at low humidities.
|
(3) Before testing the ground R.P.M. with full open throttle when determining
the need of a top overhaul, the following checks must be made:
(a) Mixture control is in full rich position.
(b) Throttle level is fully open and level has full and free travel.
(c) Spark is fully advanced.
(d) All cylinders are firing properly.
(e) Tappet clearances are .008" to .012".
(f) Magneto breaker gap is .010" to .014".
(g) Spark plug gaps are .015" to .020".
(h) Magneto attaching nuts must be tight. Loose nuts may allow the magneto to
move thereby altering timing. Magneto coupling bolts must be tight.
(i) Be sure that the fuel flow to the carburetor is not obstructed.
Clean strainers in fuel system.
(j) Check the compression of each cylinder on the engine after it has cooled
down. If the compression is satisfactory, a top overhaul is not indicated
and either the ignition or fuel system is at fault.
(4) If an engine ahs been properly taken care of, a top overhaul should not
be necessary before 200 to 250 hours of flying time, and in some cases, more,
has elapsed.
(1) General
(a) A top overhaul can readily be made with dismounting the engine from the
plane. Only those tools in the tool kit furnished with each engine need be
used for this work.
(b) Be sure the ignition switch is turned "off" so that the engine
will not be started accidentally while it is being repaired.
(c) Drain the oil tank.
(2) Cleaning
(a) Remove propeller, cowling, and exhaust stacks or ring. Disconnect
or remove the battery so that there will be no danger of sparks igniting
inflammable substances.
(b) Place airplane in a well ventilated spot where the fire hazard will be
minimum.
(c) Clean engine with suitable cleaning compound.
Caution |
On account of the fire hazard, do not attempt to wash the engine
before it has thoroughly cooled.
|
(d) Allow the cleaning compound to vaporize for the exterior of the engine.
(3) Operations Preliminary To Disassembly
(a) Place airplane in a protected dust free location which has good lighting.
(b) It will be necessary to climb around the engine installation so suitable
scaffolding and padded ladders would be of great assistance.
(c) The work bench should be located in a clean place with plenty of light.
1. General
(a) New gaskets should be installed.
Note |
If new gaskets are not available, be careful in removing the old ones, and
immediately place them between two wooden covers to prevent their drying and
cracking.
|
(b) Have plenty of clean lintless cloth on hand. Never use waste ravelings to
wipe parts of an engine because they tear loose and may cause damage later on.
(c) All tools should be listed and each must be accounted for upon completion
of the job.
(d) As parts are removed, they should be placed upon the bench in an orderly
manner and marked or tagged so that they will be returned to the proper places
during reassembly.
(2) Disconnect all ignition cables from the spark plugs.
Note |
In order to facilitate reassembling, it is advisable to tag and mark each
cable as it is taken off the cylinder.
|
(3) Remove all spark plugs.
(4) Remove rocker arm housing covers.
(5) Remove all intake pipes by unscrewing the two nuts with which each is
attached to the cylinder.
(6) Removing Cylinders
(a) On engines which use palnuts to lock the cylinder hold down nuts in
place, care should be taken in removing them. Be sure that these palnuts are
removed with a wrench, and are never forced off by turning the cylinder hold
down nuts.
(b) The cylinders are detached by unscrewing the cylinder hold down nuts with
the cylinder base nut wrench. The two rear nuts (those between the cylinder and
the induction housing) are the most difficult to reach and should be removed
first. The six nuts remaining may then be removed.
(c) Remove cylinders, pistons, push rods, and push rod tubes in the order of
rotation, leaving the cylinder containing the master rod piston (cylinder No. 1)
until last.
Caution |
In performing this operation, great care must be taken that the rods
or pistons do not drop against the crankcase and become marred or
dented.
|
(d) As each cylinder is taken off, push out the piston pin immediately and
remove the piston. If it is necessary to drive the piston pin out of the piston,
a soft drift should be used, and the piston supported in such a manner that no
dr1ving thrust is taken by the connecting rod.
(e) Never allow the piston or rod assembly to slap against the sides of the
crankcase or mounting studs after the cylinder has been removed from the
crankcase or while the crankshaft is being rotated.
(f) Secure seven pieces of rubber hose whose I.D. is large enough to
encompass the entire section of the connecting and link rods and long enough to
extend from the piston to the wrist pin. Cut these pieces along one side and
install them over the connecting and link rods immediately after each cylinder
has been removed.
(g) All parts so dismantled from the engine should be laid on a clean bench
in the order in which they are removed.
(h) While overhauling the cylinders, cover the crankcase openings with clean
pieces of cloth for protection against dust and dirt.
(7) Remove the oil screen and inspect for metal chips, dirt, etc. If metal is
present, a thorough search for the source must be carried out, and steps taken
to correct the trouble.
(1) Inspect the crankshaft and connecting rod assemblies for abnormal wear,
safe tying of retaining members, etc., through cylinder base holes in crankcase.
(2) Inspect cowling panels, fasteners, etc. for defects. Repair if necessary.
(3) Inspect propeller for nicks, burrs, fit, etc.
(4) Inspect exhaust ring or stacks for cracks, leakage at joints, condition
of gaskets, etc.
(5) Remove carburetor from engine and service check in accordance with
carburetor manufacturer's instructions.
(6) Completely service check the magnetos in accordance with the magneto
manufacturer's instructions.
(7) Replace all spark plugs with new or reconditioned plugs. Carefully
inspect the entire ignition harness for serviceable condition.
(8) Inspect all cylinder hold down studs. Remove all cylinder hold down studs
that are loose, broken, or have damaged threads. Replace with the proper
oversized studs.
(9) Check entire engine and ascertain that all nuts are tight in accordance
with torque values set forth in the table of limits. See that all safetying is
complete and tight.
(10) Inspect, tighten, and safety all engine mounting bolts.
(1) Rocker Arms
(a) On all engines, it is not necessary, nor is it desirable to remove the
rocker arms in order to grind the valves and they should be taken apart only
when some part is damaged or indicates wear.
(b) If a rocker arm roller is stuck or shows signs of wear or excessive
clearance, it should be replaced. A new roller can be fitted into a rocker arm
by an authorized service station equipped with proper facilities.
(2) Grinding And Replacing Valves
(a) Determine which valves are leaking and need lapping by pouring gasoline
into the valve ports. Valves which leak must be lapped or replaced.
(b) Removing Valves
1. Place the cylinder over a block of wood which should be 4-1/8 inches in
diameter, 9 inches high, and rounded at its upper end to fit, approximately, the
cylinder dome. It is best to have the block attached to a wooden base, so that
it stands upright on the work bench. This block serves to hold the valves closed
while the springs are being removed.
Note |
The valve supporting tool in the engine tool kit may be used for the same
purpose; but the wood block will prove the more convenient when the cylinder
has been removed from the engine.
|
2. Remove the rocker arms and shafts in order to install the valve depressing
tool. Depress the valve springs with the valve spring depressing tool. Remove
the split cone, the valve washers, and the springs. Care must be taken to keep
the valve washers and valve retainers separate as different units are used.
3. To avoid damaging the valve guide when removing the valve, inspect the end
of the valve for burrs. If any are found, they must be removed.
(c) Reconditioning and Valve Grinding
1. After both valves have been removed, scrape off all carbon from the
cylinder dome and from the valves, being careful not to mar or scratch the valve
seats and the valve stems.
Note |
A simple and handy fixture for holding the cylinder while grinding the
valves or cutting the valve seats as described under "Complete
Overhaul" , is a 6" x 12" steel plate 1/8" thick, with a
4-7/8" hole near one end of the plate. Such plates may be purchased from
the Warner Aircraft Corporation. The cylinder should be attached to these
plates with two 5/16" diameter bolts holding the cylinder flange to the
plate. The other end of the plate should be held in a vise.
|
2. To grind the valves, spread a small amount of valve grinding compound
around the seat of the valve, insert the valve in the guide and grind with the
valve grinding tool from the engine tool kit. Repeat the operation until a good
seat is obtained.
3. Wash the valves and the cylinder carefully with gasoline so that no trace
of the grinding compounds remains.
4. Inspect valves with magnifying glass for cracks.
(d) Reinstalling Valves
1. Put the valves in place, being careful not to interchange those of
different cylinders. The cylinder number is etched on the valve stem below the
groove.
2. Put the cylinder over the wooden block tool used for disassembling.
3. Snap the circlets, where used, into their grooves from the side, and
assemble the lower valve spring washer, the springs, and the upper washer to the
head.
4. Depress the valve springs with the valve spring depressing tool. Insert
the two halves of the split retainer, being careful that the proper type
retainers and upper washer are used. Be sure that the two retainer halves used
on each valve, if numbered, bear the same number.
5. After the valves have been assembled, they must be tested with gasoline
for tightness, and if they still leak, the valve grinding must be repeated until
they are tight.
(3) Cylinders and Heads
(a) Check cylinder bores for out-of-round, taper, scores, cracks, etc.
(b) Check cooling fins for cracks, etc.
(c) Carefully check the fit of the spark plugs in the cylinders. Carbon in
the threads or the effect of frequent heating and cooling may cause the plugs to
become tight. If such is the case, retap with a special tap which can be
procured from the Warner Aircraft Corporation.
(4) Pistons, Piston Pins, and Rings
(a) Cleaning and Servicing Pistons
1. Remove all the rings from the piston by spreading the ends apart until
each ring can be pulled out of its groove over the top of the piston.
2. Scrape the carbon from the top surface of the piston and then polish by
rubbing it on a piece of kerosene soaked crocus cloth, spread on a flat plate.
3. Remove all carbon from the ring grooves.
4. Inspect the piston for cracks and scores.
5. If there are any sharp edges or scratches on the pistons or in the
cylinder wall surfaces, they should be carefully removed by stoning with a fine
grade oil stone which has been dipped in kerosene.
6. When a defective piston is replaced, the new piston must be selected so
that its weight does not differ more than 1/4 ounce from the others. When
ordering pistons for replacement, please state the engine number. Records are
kept of the weights of the pistons originally furnished in the engine.
Therefore, pistons of the proper weight can be shipped when the engine serial
number is furnished.
(b) Servicing Rings
1. Remove all carbon from rings and make sure that they are not damaged.
2. If the engine is equipped with expander type oil rings, it is highly
recommended that new expanders be installed at the top overhaul in all cases;
rings and shims showing no scratches or other signs of wear may be
reinstalled. The use of new expanders greatly facilitates the reseating of
the ring. Best results may be derived from the top overhaul if a new complete
expander type ring assembly is installed.
3. Test tension of rings. Refer to the table of limits.
(c) Piston Pins
1. If plugs are loose install new ones.
2. Magnaflux pin to check for cracks and possible failure.
3. Check for fit in piston and connecting rod bushing.
(5) Installing Piston Rings
(a) Be sure that all parts are absolutely clean and in good condition.
(b) The ring gaps must be staggered so they do not line up causing blow-by
with excessive oil consumption.
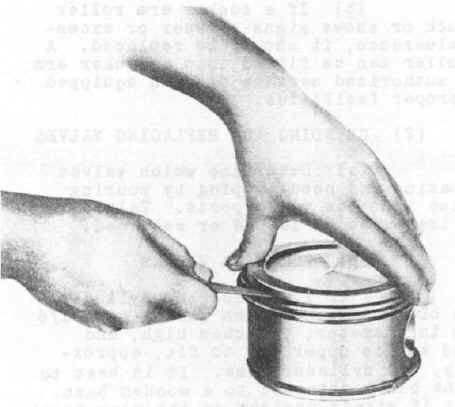
Figure 4. Checking Piston Ring Side Clearance in Piston.
(6) Assembling Rings To Four Ring Pistons
(a) The rings furnished by the Warner Aircraft Corporation are fitted and
inspected in regard to the proper gap width. See Table of Limits for this
width.
(b) The fourth (bottom or oil control) ring must be placed on the piston in
such a manner that on pistons No. 1, No. 2, No. 3, and No. 4, the ring gap is on
the exhaust side of the cylinder. In other words, when looking at the top of the
piston with the number on the piston toward the observer, the ring gap should be
to the right and at right angles to the piston pin. On pistons No. 5, No. 6, and
No. 7 the arrange is reversed. The ring gap should be on the intake side (to the
left when looking at the top of the piston when facing the numbering).
(c) The rings must have the side clearance and gap specified in the Table of
Limits (see Figures 4 and 5).
(d) All rings must be installed to obtain approximately 90 degree spacing
between the four gaps of the rings on each piston.
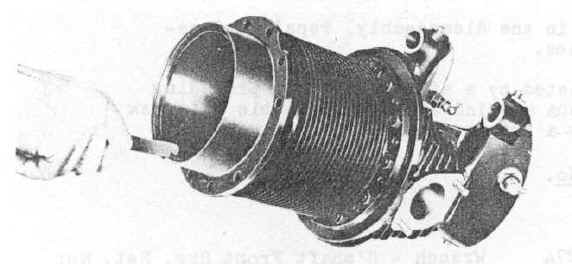
Fig.5 Checking Piston Ring Gap (Closed) in Cylinder Barrel
(7) Assembling of Pistons to Cylinders
(a) It will be found advisable, if new rings are assembled to the piston,
that because of the tight fit of the rings, the piston be put in the cylinder
while it is on the bench.
(b) Oil the piston generously.
(c) Use a piston ring clamp to hold the rings in place. Great care must be
taken when putting the piston ring clamp on the piston that the rings actually
slide into the grooves while the clamp is slowly tightened. To help the rings
slide into the grooves, the clamps should be lightly tapped with a block of wood
or the end of a screwdriver.
(d) Holding the numbered end toward the propeller end, the piston should be
pushed in to such a depth that all the rings are in the cylinder, but not so
deep as to cover the piston pin hole. The piston pin can then be pushed in while
assembling the unit to the engine.
(8) Assembling of Cylinders and Pistons To Engine
(a) Install new cylinder base "0" ring packings on cylinder skirts
or new cylinder base gaskets on the cylinder mounting pad on older type engines.
(b) Turn the crankshaft to a position in which the connecting rod of No. 1
cylinder extends the maximum distance outside the cylinder flange and the cam
followers are in the lowest position.
(c) Holding the cylinder assembly, line-up the piston pin hole in the piston
with the bushing in the rod and with the number on the edge of the piston facing
the propeller. Insert the piston pin.
(d) Push the cylinder on to the piston so that it is even with the bottom of
the piston skirt. When installing cylinder, squeeze the fourth ring, if
provided, with the fingers.
(e) Slip a steel washer between the new packing and the shoulder on the inner
end of the push rod tube.
(f) On the outer (longer) end, assemble the spring, the washer, and the
packing, in the order given. In the event the spring may have taken a set, two
packings may be installed to increase the spring tension. This is only possible
on the push rod tubes which do not contact the packed cam follower guides.
(g) Dip both ball end of each push rod into the rocker arm grease then place
the push rods into the tubes with marked end toward the rocker arms. The rods
are marked alphabetically, starting with "A" for the exhaust side of
the cylinder No. 1 and follow around the engine clockwise order, as viewed from
the rear.
(h) Holding a push rod tube assembly in each hand, push the cylinder into
place on the crankcase with the body, at the same time guiding the push rod
tubes into place.
Note |
The long end of the push rod tube with the spring, washer, and packing is
inserted into the head of the cylinder.
|
(i) Install and tighten cylinder hold-down nuts using cylinder base nut
wrench. Tighten nuts with desired torque as outlined in the Table of Limits.
Caution |
Do not exceed torque limits.
|
(j) When palnuts are used, they should be tightened only 1/4 turn after
coming in contact with the cylinder hold-down nuts.
(k) After cylinder No. 1 has been assembled to the crankcase, all other
cylinders should be assembled in numerical order in the same way.
(l) On the intake pipe install, in the order named, the spring, gland, and
new packing.
(m) Install new gaskets on the intake flange of the cylinder.
(n) Insert the end of the intake pipe into the induction housing opening, and
push the flanged end into place over the studs.
(o) Install a plain washer, lockwasher, and nut on the inside stud of the
intake pipe flange and an ignition wire clip, lockwasher, and nut on the outside
stud. (Ignition cable clip is not used when Breeze shielding is installed).
(p) Tighten the intake pipe flange nuts to the required torque.
Note |
The ignition cable clips must be in a position with the open end facing
out.
|
(q) Set all valve tappets.
(r) Install spark plugs and attach ignition wires.
(s) Take off crankshaft turning bar.
(t) Connect battery.
(u) Install exhaust stacks or collector ring.
(v) Install cowling.
(w) Install propeller.
(x) Fill fuel and oil tanks after replacing drain plugs.
(y) Inspect according to instructions in Section VII.
(z) Start and run in accordance with instructions in
Section XI.
|